What is modular construction?
Modular construction has become something of a buzzword in the architecture, engineering, and construction industry. At its most basic level, modular construction refers to components fabricated off-site in a factory setting and assembled on site during construction. This broad definition means you may hear it being used to describe elements of various scales, ranging from individual building components to full-scale buildings.
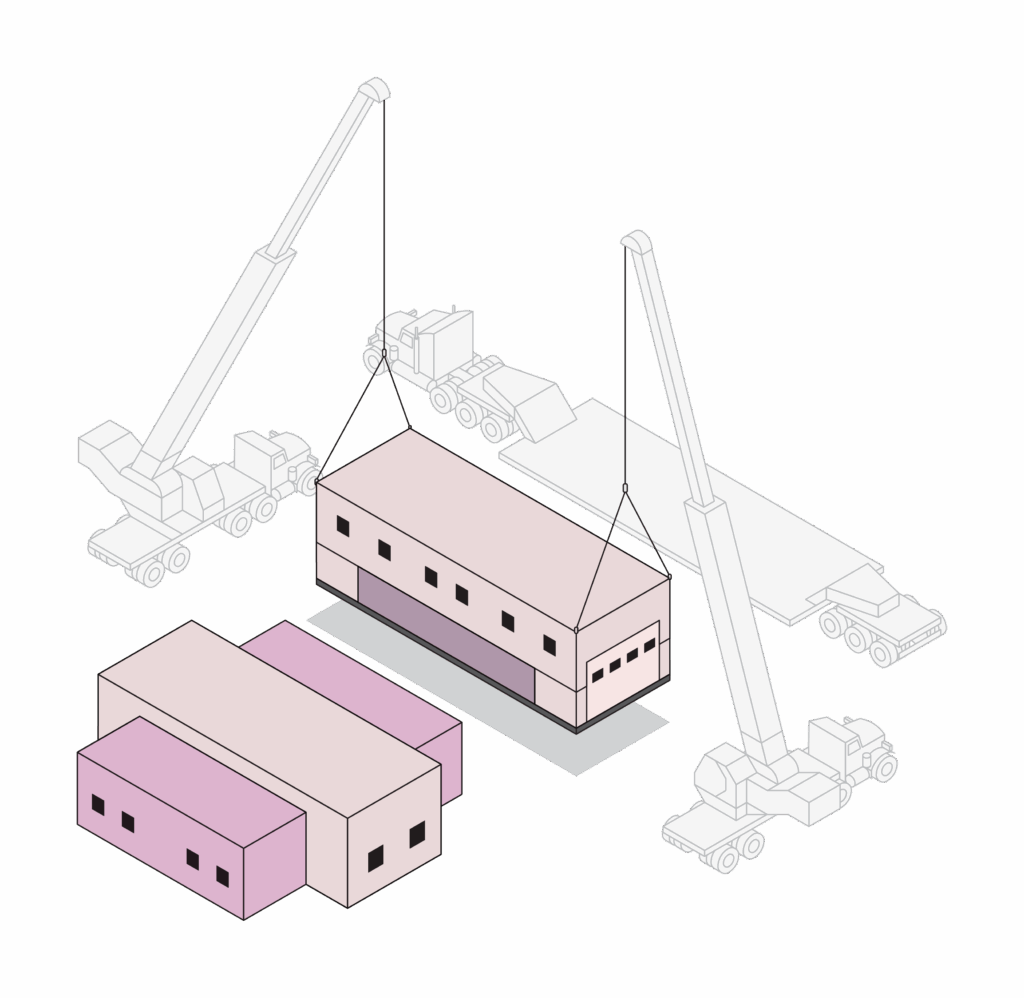
Although modular construction is not a new concept, the excitement around it lies with the expanding capabilities of manufacturers and the ability to leverage efficiency, precision, and repetition to reduce cost and time in building construction. This helps address some of the key issues facing the construction industry today:
- high construction costs
- reduction of skilled trades
- long timelines for construction
- procurement uncertainty for materials
The term “modular construction” can be applied to components that have always been required to be fabricated off-site, such as individual glulam members. However, at the current level of the technology, innovative fabricators are now able to deliver multi-material assemblies (such as exterior wall panels complete with cladding, insulation, and membranes), or even prefabricated building bays craned and placed on pre-installed foundations, with architectural work required to seal the modules together and coordinate the off-site and on-site elements.
f-BLOK recently completed a firehall for the City of Winnipeg using this method. The project is a complete multi-bay modular building that allowed us to experience the benefits of this approach: shorter timelines, controlled factory conditions for fabrication, and the ability to deconstruct and relocate the building as needed to serve growing communities.
What are the benefits and complexities we see with modular construction?
Modular construction is gaining traction in the industry as it addresses several shortcomings of the traditional design/construction process. We find that now more than ever, clients are looking for ways to tighten the construction schedule and deliver projects in shorter timelines that allow them to quickly react to the demands of the market or the needs of a community. Additionally, ongoing uncertainty around the procurement of materials and products means that projects can be susceptible to pricing fluctuations. Utilizing modular construction in projects helps address these issues.
When any new process is introduced to the construction industry, it’s not without its challenges. Some of the nuances of utilizing this process include:
- Components manufactured off-site in a different municipality or province may not meet local code or zoning requirements.
- Transporting large components to site involves logistical complexities.
- Off-site components must be precisely coordinated with on-site elements, such as foundations, to ensure seamless assembly.
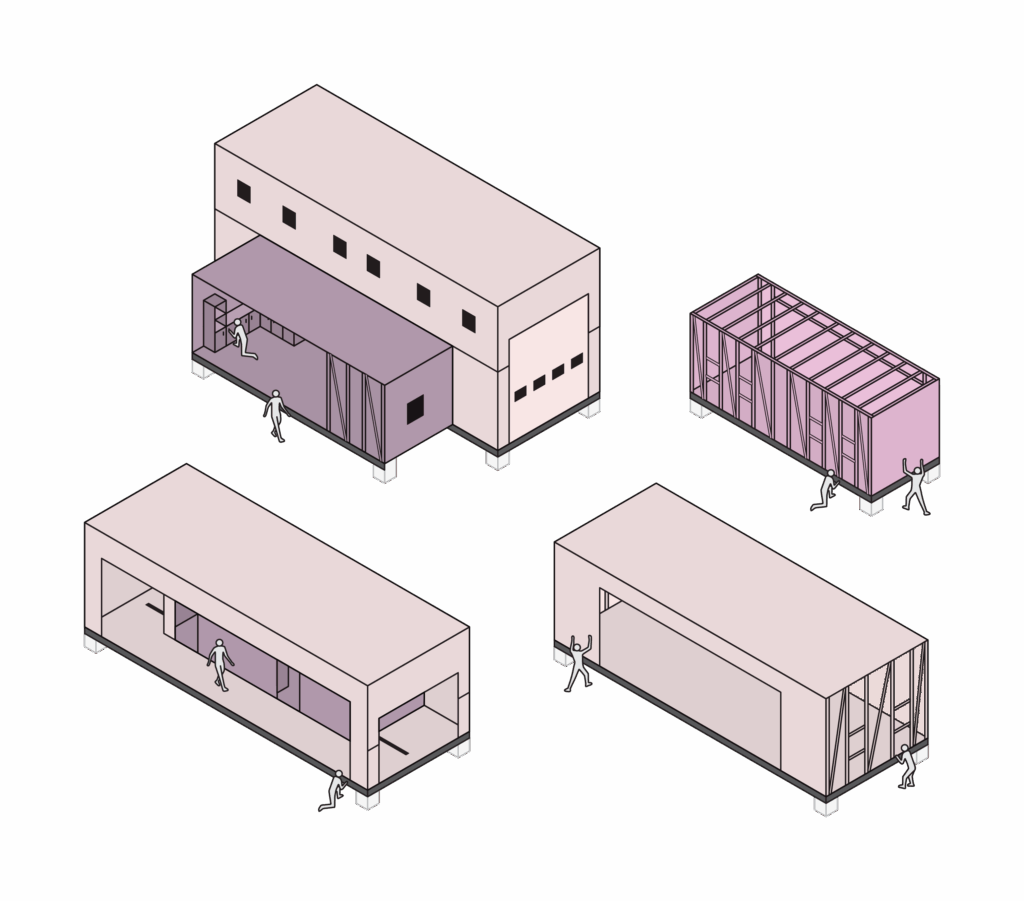
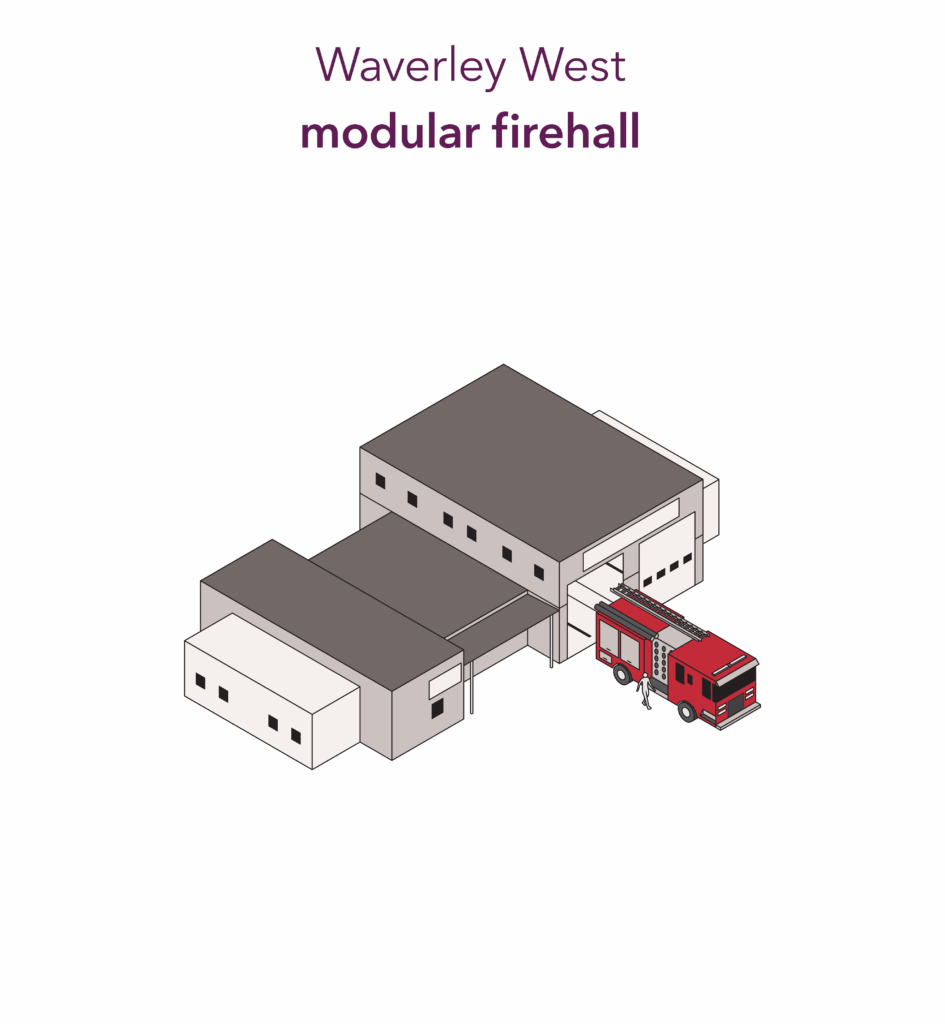
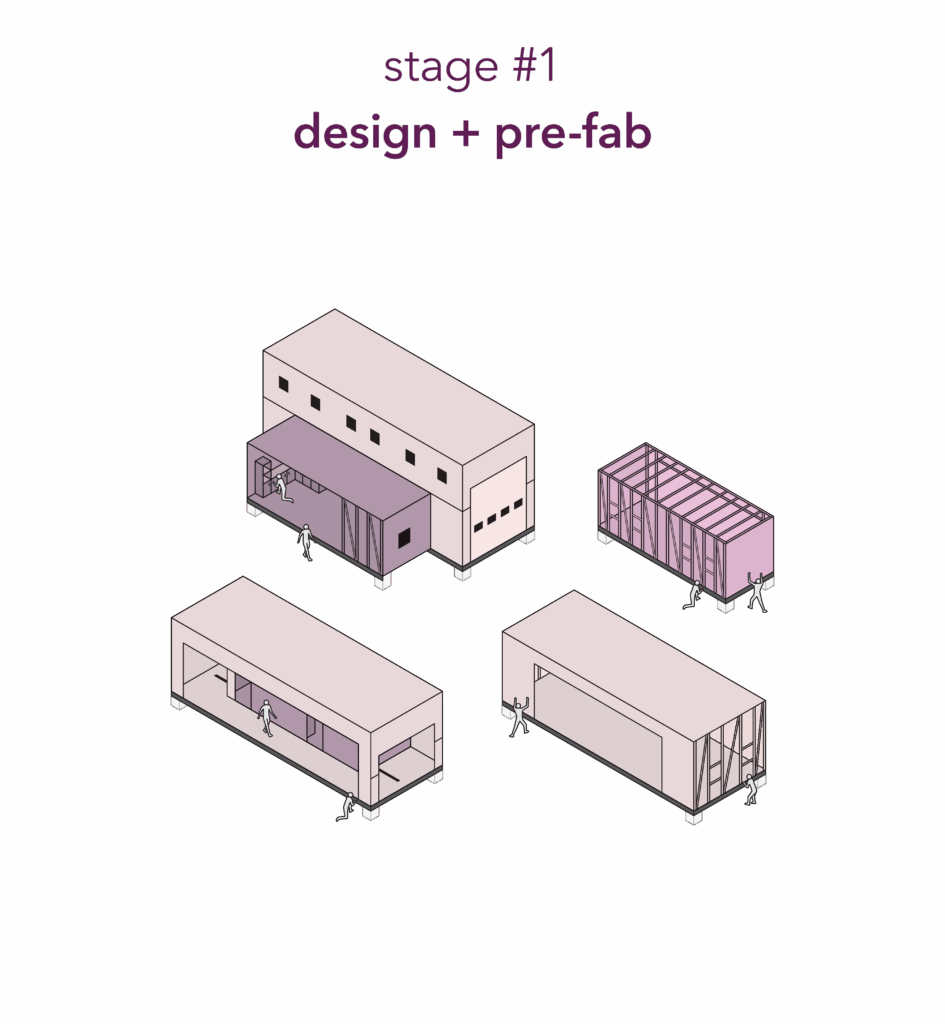
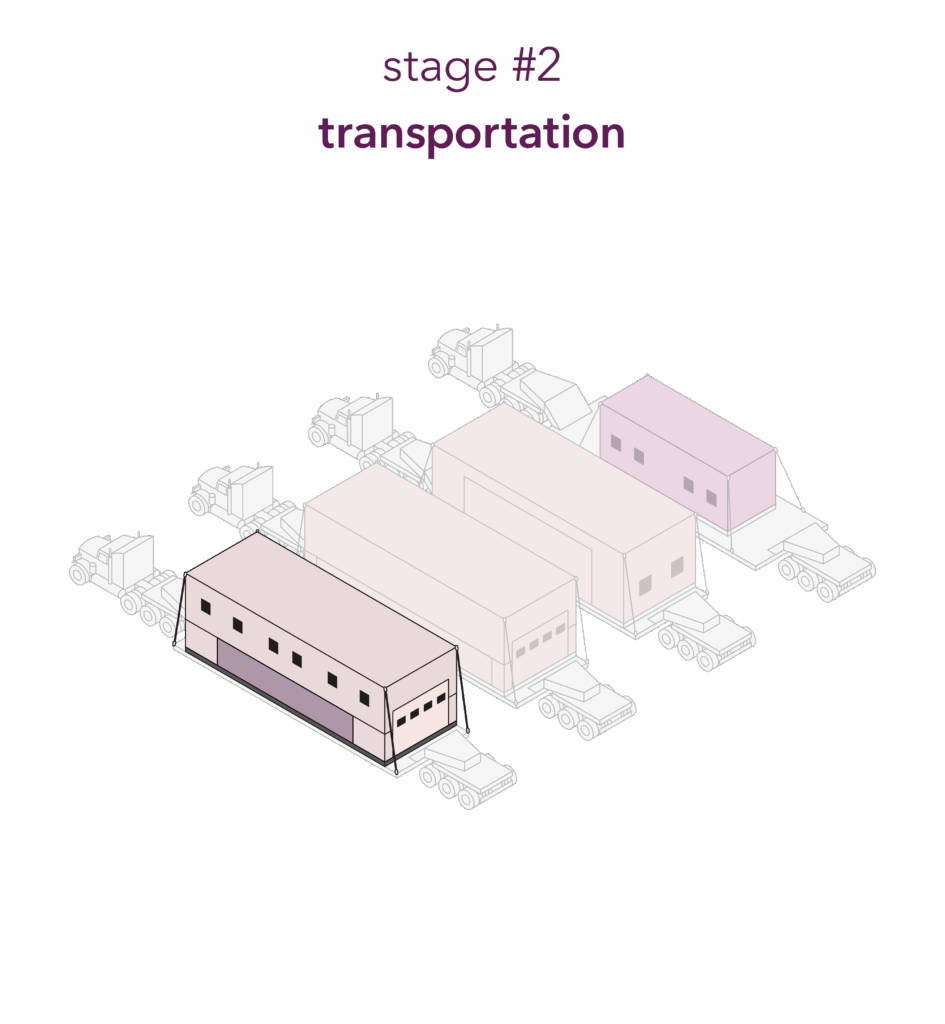
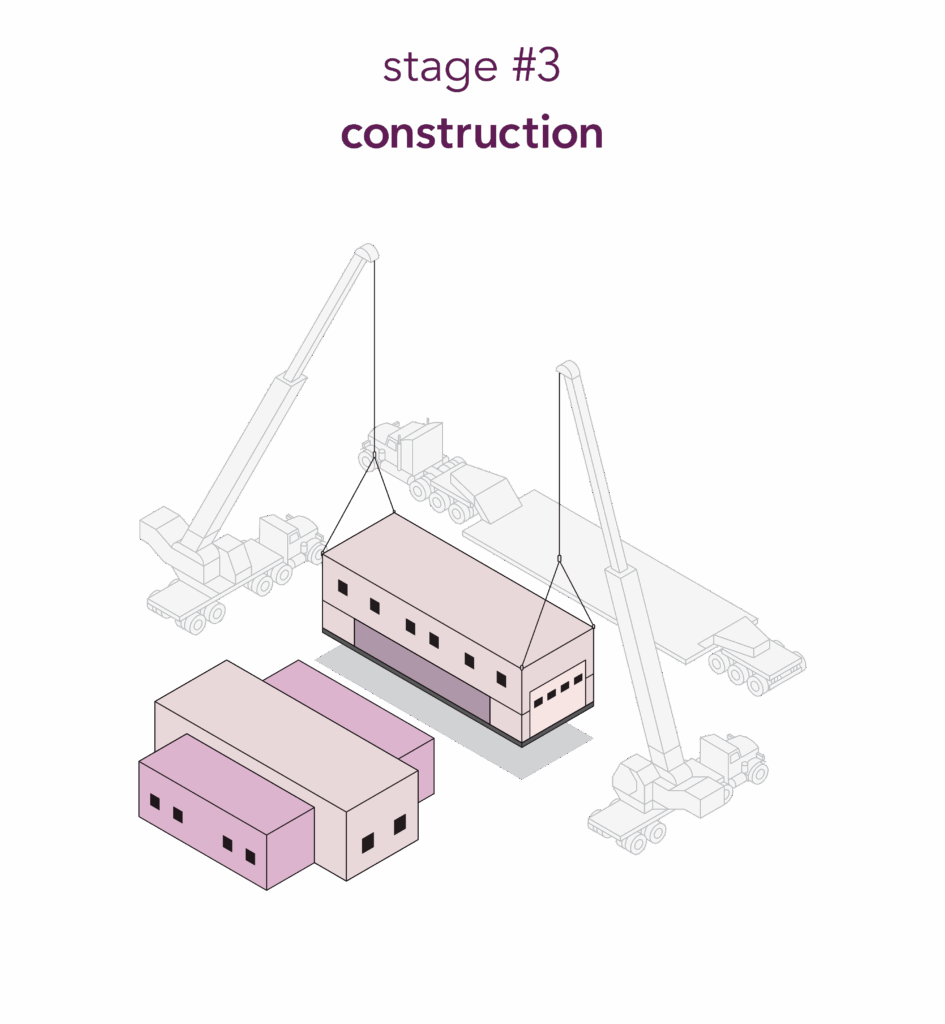
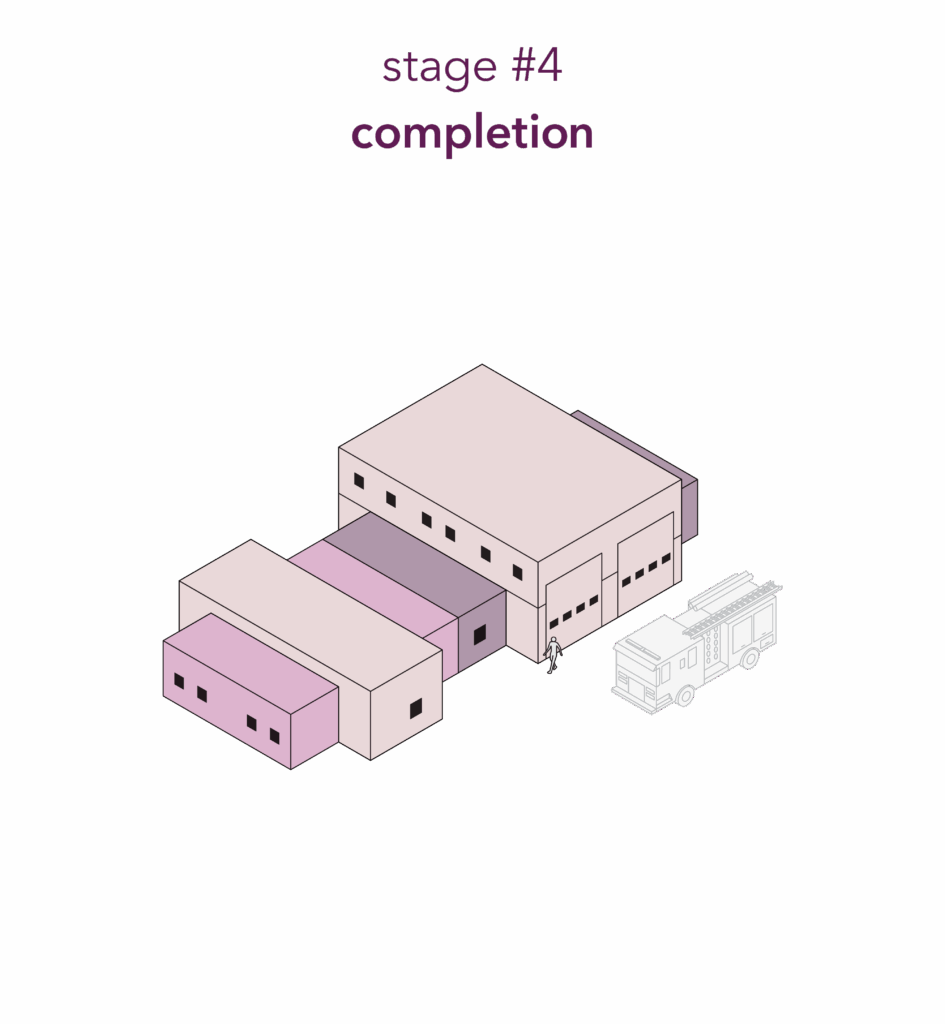
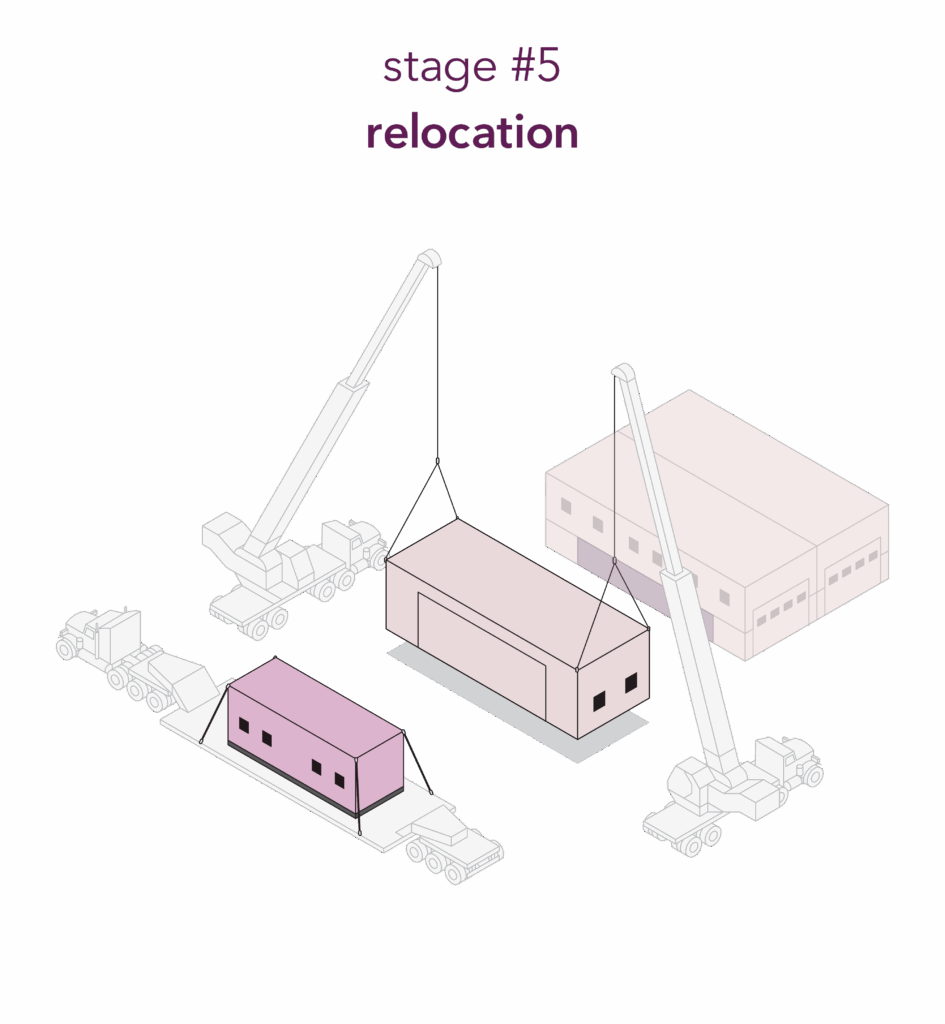
How has f-BLOK successfully applied modular construction to real-world problems?
In late 2023, the City of Winnipeg decided to pursue a modular firehall building approach for the community of Waverley West. f-BLOK, together with Tractus Projects as contractor and Extreme Modular Buildings as fabricator, were responsible to deliver the modular firehall.
The modular solution was chosen for this community as it would provide immediate services in the Waverley West community while design and construction of the permanent firehall, expected to take several years, was underway. Once the permanent firehall is constructed, the modular building can be transported and redeployed for use in a different area within the city facing similar needs. f-BLOK coordinated the process, ensuring adherence to City of Winnipeg standards, fire department requirements, and zoning and building code regulations.
The building was fabricated off-site as seven distinct bays. There were three primary modules, each 50 feet long, that were heavy, over-dimensional, and required a night move and police escort into the City of Winnipeg. Two of these primary bays also had additional bays nested within them that were pushed outwards after transportation. Additionally, two secondary modules were transported from factory to site with more typical step deck trailers. These modules were placed on a foundation consisting of 80 screw piles located along the perimeter of the bays. Significant coordination was required to situate the screw piles to align with structural components of the modular units. After all modules were placed on site, the bays were joined together. Lapped membranes and flashing on the exterior created a watertight envelope and floor and ceiling finishes were infilled between bays on the interior to make one cohesive building.
The modular firehall for Waverley West was completed in approximately one-third the time required for a traditional design/construction process. Once it is no longer needed in its current location (upon completion of the permanent firehall), the City of Winnipeg can disassemble the modular building and move it to a different community in need within the city essentially overnight. This pilot project demonstrated to the City the ability of modular buildings to fill a need and opens the door to similar solutions for other neighbourhoods.
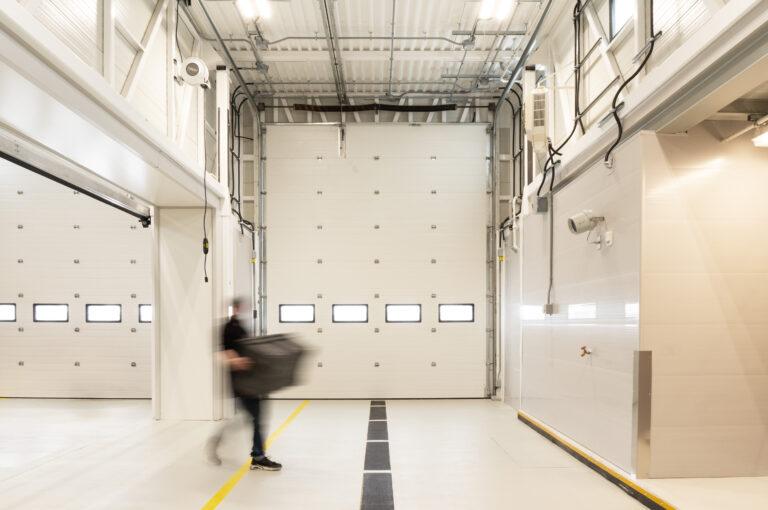
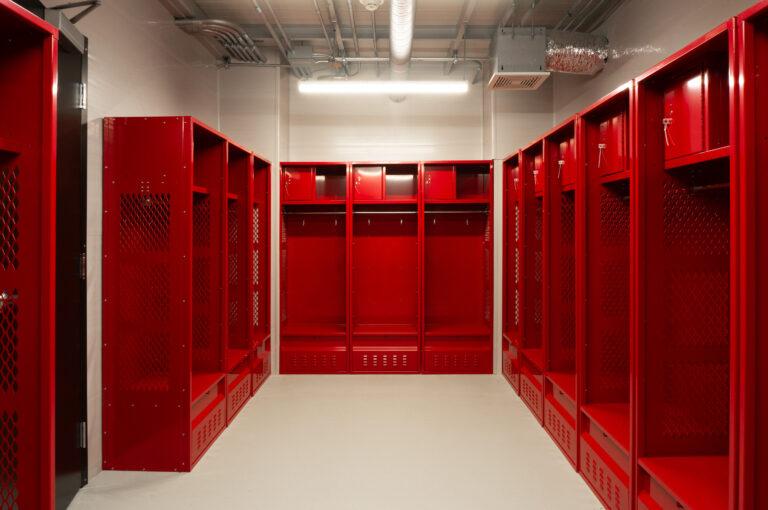
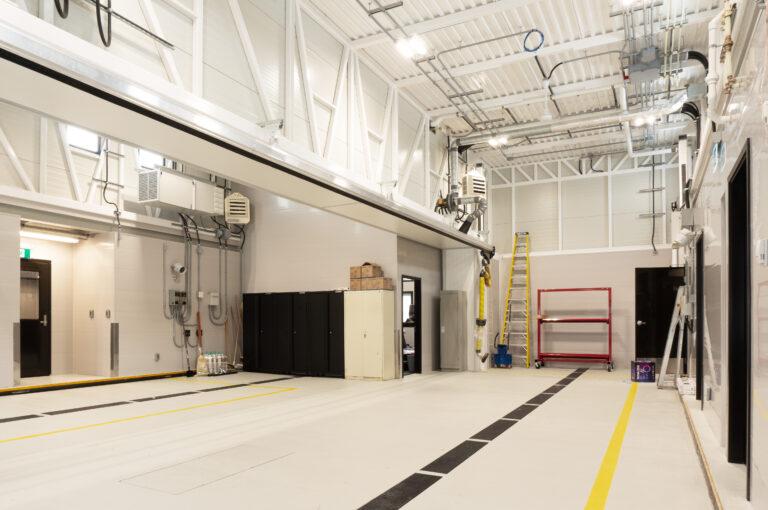
What’s the next buildingBLOK in modular construction?
Modular construction is a growing field in the architecture, design, and construction industry. It allows for many benefits, including reduced timelines, flexibility in disassembly and transport, as well as minimized material waste. As materials are fabricated to shop-level tolerances during fabrication, minimal waste is created. Any products or materials that can be recycled are recycled within the shop environment. There are also economic benefits, as the portability of these buildings means they can be disassembled and deployed to future communities, minimizing construction costs for those areas.
f-BLOK has demonstrated our ability to navigate complexities regarding code/AHJ requirements and standardized prefabricated components. Through careful coordination and communication, we help clients overcome the obstacles that may be holding them back from pursuing modular construction for their project.
If you’re interested in exploring how modular construction might be a fit for your project, reach out to us—we’d love to help you put the pieces together.